Enhancing resilience in today’s digitalized and automated ships.
FS Coating has protected cables for more than 30 years on board ships and in the oil and gas industry. Initially, only fire protection was performed but over the years more benefits and a wider scope of work have been added.
Over the years vessels have experienced enhanced resilience in vessel electrical systems by protecting the cables with FS coating as a means of protection. Relatively new is certified coating systems from Fire Security which upgrades cables fire technically to flame-retardant and fire-resistant standards among others.
The ship’s station keeping ability as well as the ability to continue to operate as designed is greatly enhanced by keeping the cables operational in a fire situation.
FS Coating of cables extend the lifetime of existing cables, this being from general protection of the cables in normal conditions and specialized protection in certain harsh areas. Fire Security also has coating approved to repair cables’ outer sheath.
This is a major benefit as the repaired cable will be upgraded fire technically as well as protected from the environment.
The following industry segments have traditionally been the main users of the FS technology:
- Cruise Ships
- Offshore oil and gas platforms
- Drilling rigs
- LNG Carriers
- Floating Production and Offload ships (FPSO’s)
- Tankers
- Ferries
- Power Plants and Substations
Typical causes of a cable’s normal ageing are identified as:
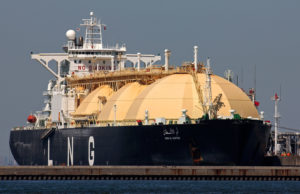
In recent years we have protected cables on numerous LNG tankers. We also do cable repair and extension of their operational life.
- Ultra Violet rays from the sun (UV)
- Ozone in the atmosphere
- Oxygen in the atmosphere
- Tropical environment
- Specific vessel or site environment may be chemicals, heat, mud, etc.
FS Coating of cables may contribute to a large risk reduction of any Ship or installation, the main factors of a reduced level of risk derived from the coating of cables are listed below.
A) Fire risk, fire scenario.
- Limit the risk of a fire starting from the cables themselves.
- Avoid cables as a way of spreading fire.
- Keeping the cables live in a fire situation and thus maintain control, surveillance and communication.
- Prevent the development of smoke and toxic gases from burning cables.
- Reduce the overall fire load in any area with cables.
B) Normal operation
- Maintain the insulation levels in the cables
- Prevent cracks from developing in the cables.
- Prevent water or gas ingress.
- Increase the resistance of the cables to chemicals.
- Delay the natural ageing of the cables.
Fire protection and cable life extension.
Fire Security’s coating systems have the ability to upgrade the cables fire technically and at the same time extend the lifetime of the cables without any shutdown required gives you huge flexibility when maintaining or upgrading an existing ship.
Author: Leif Harald Tveitnes, President at Fire Security